Scott Storey, Klismos2021 (STUDENT 2022)
- Student:
- Tertiary
- Name of school or tertiary institution, and name of woodworking teacher (if you have one):
- Centre for Fine Woodworking, tutor: David Haig & Tony Clarke
Description: Chair Name: Klismos2021 Concept: To create modern Klismos chair • To keep the distinctive shape of a Klismos chair • Create a more functional chair by reducing the protruding legs that limit maneuverability • Create a simple yet classic looking seat • A sturdy and elegant chair Wood Used: American Black Walnut American White Ash Techniques used: • • Drawing plans: To help solve design issues • Modelling: Scale and full size to understand compound angles and production • Making jigs and Forms: For cutting and gluing seat segments. For the stacked laminations of the bent back rest. • Timber Selection: Selecting timber that is suitable for the purpose, noting the end grains radial pattern and length grains imperfections, to limit wood movement, structural failure and machining issues while maximising aesthetics. • Milling: Jointing, planing and table sawing to create clean faced symmetrical timber • Cutting seat segments: Using gig and planing if necessary. • Gluing seat segments together: Domino joinery is used. • Shaping timber: Create templates using bandsaw, table saws, scrapers and spokeshave. Band sawing excess away from pattern leaving only 1-2mm to be removed on the router table. Due to the curvatures involved, pieces needed to be routed from deferent directions because of grain issues. Cutting the seats shape. Cutting & jointing laminations for the back rest. Thickenessing laminations. • Joinery: Halving joint for the cross over seat substructure. Mortise and tenon from substructure to legs. Made with chisel and hand saw • Stack lamination: Gluing laminations over bending form and placing in a vacuum bag to hold down until it dries. • Shaping the back rest: Jig’s on table saws and spokeshaves • Fitting back rest: Cutting a rabbet’s into the back rest with handsaw, chisels and hand router. Cutting halving joint in the upper back legs using hand tools. • Pre Assembly Finishing: Finishing visible but aren’t accessible while insuring jointed and gluing surfaces are taped to ensure a bonding surface • Assembly: Stage 1: Glue seat substructure Stage 2: Gluing legs to Stage 1. Stage 3: Glue backrest Stage 4: Attach seat • Finishing: Level legs. Scrap & hand sand. Finished Walnut with Osmo natural and Oslo white for the framing (Ash) Images: Photography by Daniel Allen from Nelson, New Zealand
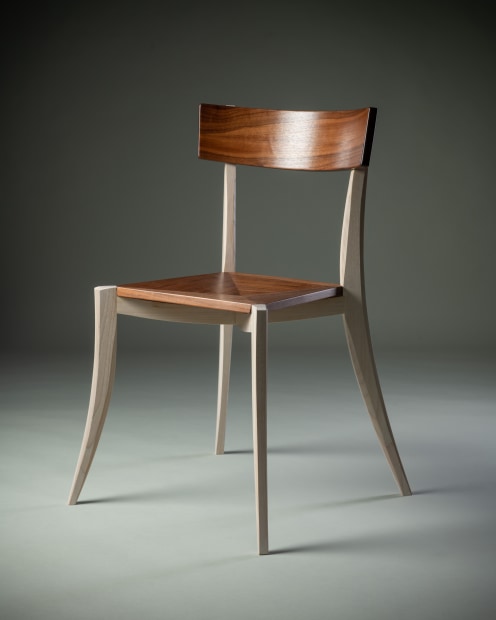
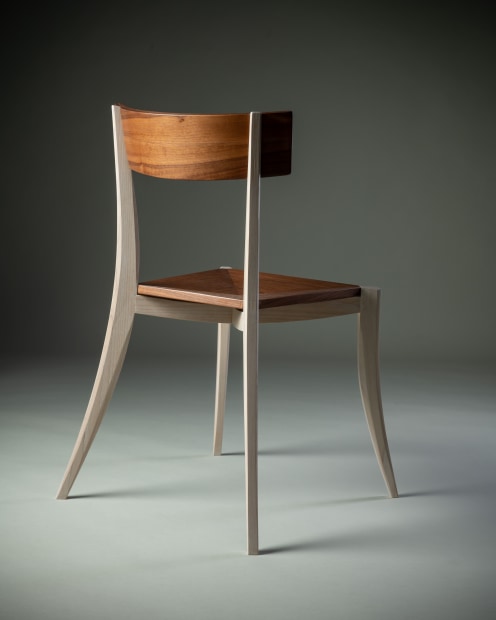
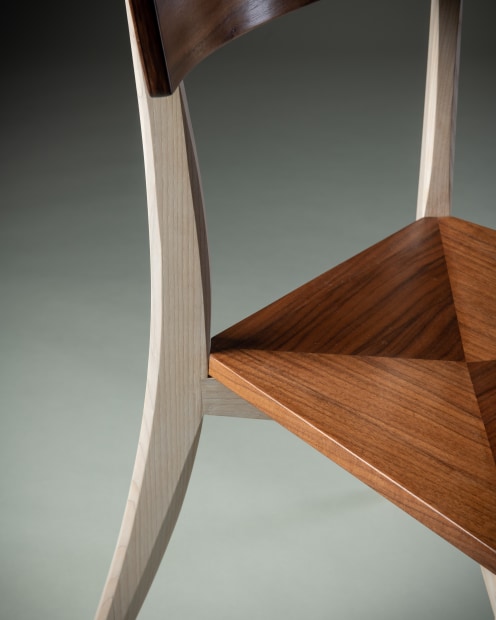
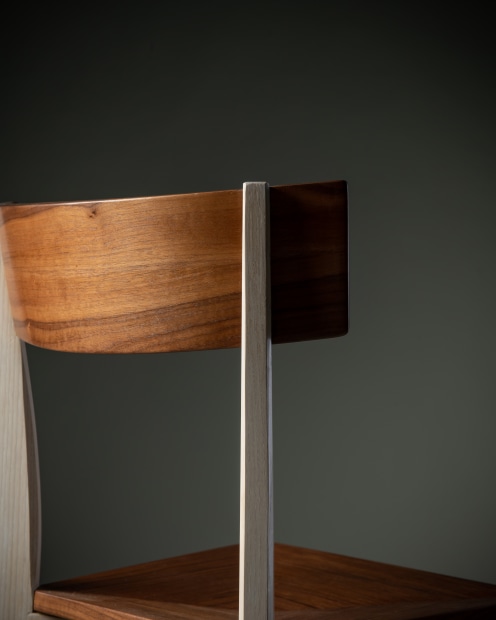
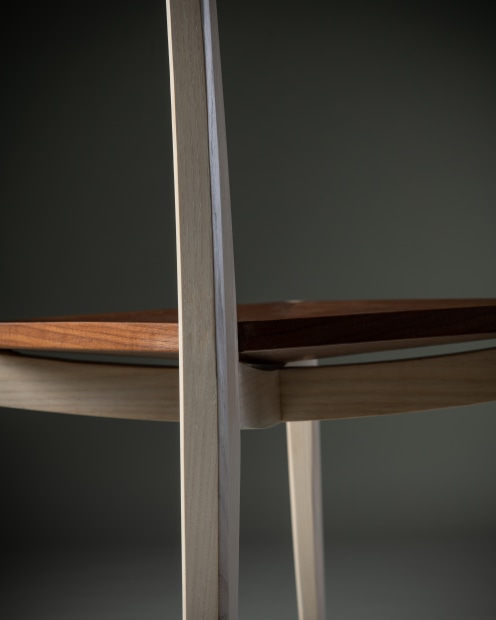
Images have been resized for web display, which may cause some loss of image quality. Note: Original high-resolution images are used for judging.