Maia Moffat, Arm Chair (Student Awards 2019)
During the creation of my armchair, I set out to create a design that could be compared with a highly successful 1960s Danish design. I believe I have achieved this throughout my design as I have incorporated an enormous amount of different skills, processes, and technologies that have the potential to go beyond the industry standard and what is expected of a HSC student. I did, however, face some big problems during the creation and design of my project, but I like to think that I came up against these problems with an optimistic attitude and figured out the solutions to overcome them. I have used all types of creative design elements and unique materials to help me provide a functional purpose for my design as well as adding an aesthetic value to the piece of furniture. From the beginning, I intended to incorporate creativity and innovation into my design which has helped push my personal ability as a designer to the next level as well as pushing the limits of what I believed I could achieve. The intricate timber skills in conjunction with the unique design elements such as the segmented backrest along with the laminated front legs illuminate the technical features which help push my project to the extremely high-quality product. Furthermore, the process of completing all of my joinery before shaping any of the timber allowed me to maintain square, parallel references which in turn helped me produce perfect, gapless joinery. The quality of my armchair can also be attributed to shaping the legs and backrest prior to gluing up on the router table and then hand shaping and blending the joints once it was together. This resulted in seamless transitions from my back legs to the backrest and cross rails to the legs. Taking the time to rebate timber into the front laminated legs and underside of the backrest was a very smart decision as it reduced the chances that the grain would feather and affect the aesthetics of the joinery. All of the time taken in planning the approach of shaping and assembling my chair has paid off and I could not be prouder of my major project. Throughout my production I have created two jigs to help me complete my processes. The first jig was created to hold my curved front legs so that I was able to route out the knuckle space without having to worry about the leg moving. The second jig I created was an exo-skeleton that I used to hold up the dry connection of my front and back legs and also by backrest. I created the exoskeleton to be able to mark out and measure the side rails and seat rails so I was able to perfect it. All jigs created were problem-free and perfectly made to the right measurements. Shaping was a hard skill to perfect as I had to make sure I didn’t shape the wrong place. It also consisted of melding solid blackwood into other rounded components to create a curved and smooth look. I used this skill on the backrest knuckles and the front leg knuckles as well as using it to blend the backrest from a solid, square piece into a curved, smooth and comfortable backrest. The overall production of designing and manufacturing my major work was a strenuous and extensive experience that I will never forget. Year 12, Freshwater Senior Campus. Teacher: Ben Percy
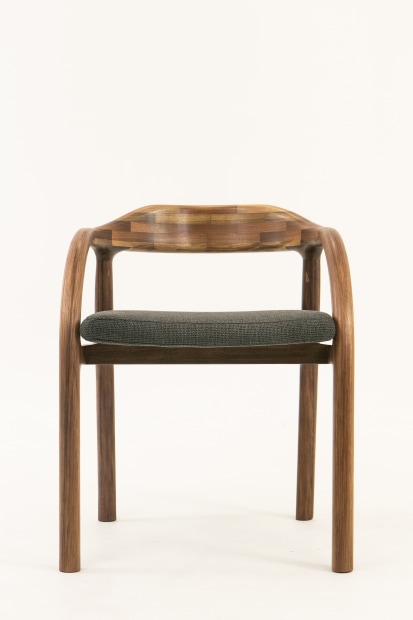
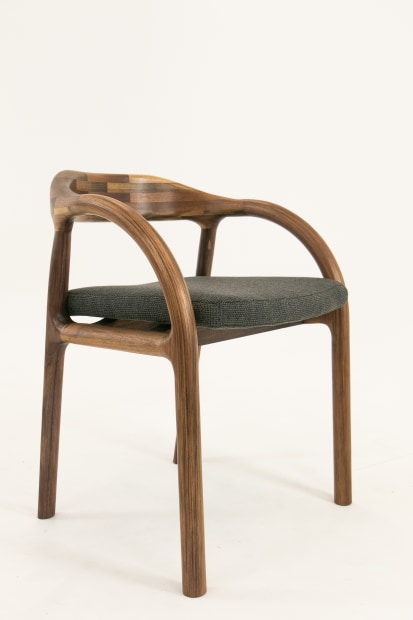
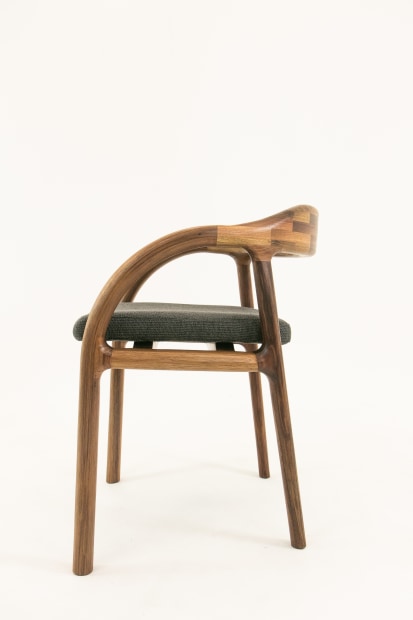
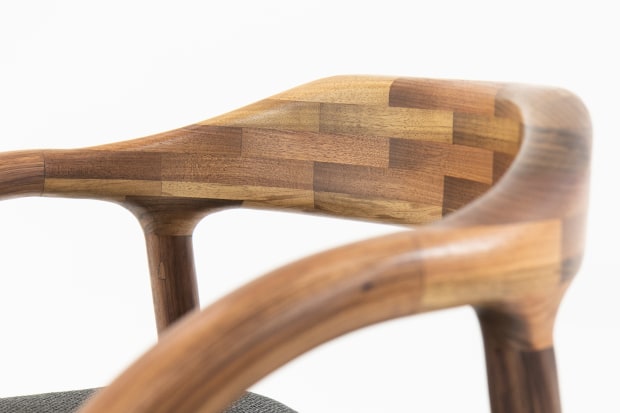
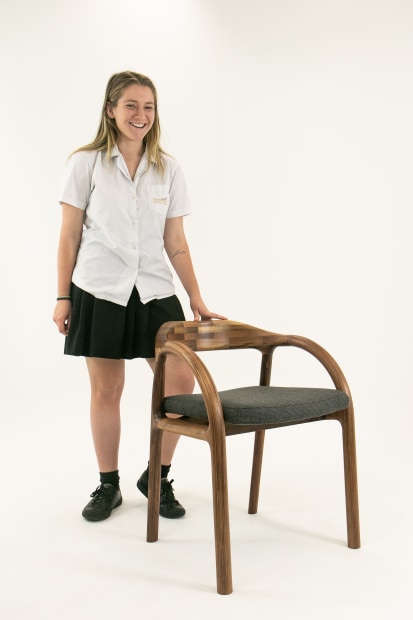
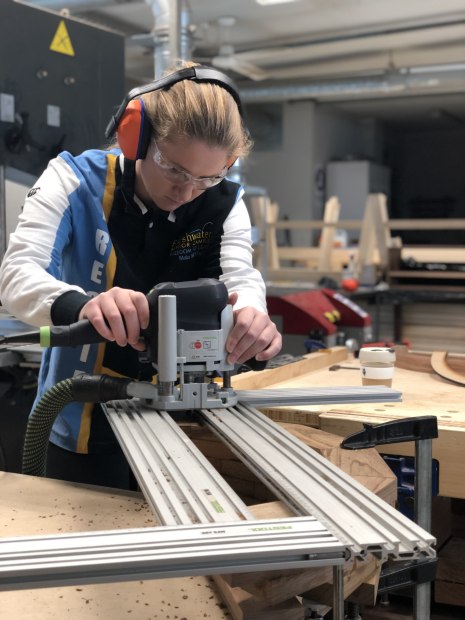
Images have been resized for web display, which may cause some loss of image quality. Note: Original high-resolution images are used for judging.