Michael Fortune: Anything but square!
Michael Fortune cutting a curved support for his Geneva Sofa Table in his workshop in Ontario, Canada. Michael’s ability to create curved and angled furniture and the jigs used in thereof is legendary.
Words: Michael Fortune
Images: courtesy Michael Fortune
Diagrams redrawn by Graham Sands
Machines and even hand tools are most comfortable creating flat surfaces at right angles to one another. Blades, fences, and tables do tilt but the starting reference is always 90°. Most technical drawings used to describe an object work with the same principle, there’s a front, top and side view all at right angles to one another.
When furniture and the various components are no longer at right angles and begin veering into curved or angled forms the construction certainly becomes more challenging. Formulas or computer programs for calculating compound inclines are available but I avoid them because the resulting numbers still have to be tried, often more than once, to the part or machine or hand tool surfaces.
Working with wood is often a subtractive process so I like to get it right first time around. I am often using steambent or laminated parts, so it’s not practical to just get another piece of wood.
Instead I’ve come to rely on a method that takes advantage of the predisposition of our tools and ourselves, to reference from ‘square’. I use this approach for one-off furniture or furniture that I may reproduce in the future. The platform and skeletons are not always required again because the jigs that have been made can be used on their own.
Exoskeletons and endoskeletons
Everything we make can fit in an imaginary crate. If the crate is sitting perfectly flat, i.e. dead level and all the sides are square to one another then the ‘crate’ can be used as the reference for measuring any angle or joint within. If it is an actual crate it will be in the way and you can’t see the surfaces or joints you wish to create. To get around this I make the crate into a frame like structure I call an exoskeleton.
With some objects an exoskeleton is not useful but an interior structure, an endoskeleton, still based on ‘square’ may be more appropriate. The skeletons are always made in a manner that allows them to be disassembled and altered as necessary once the design begins to take shape.
An important part of either method is working from a centreline. Early on I make the decision to only measure the left or right side, if both are measured they will inevitably be slightly different. That will undoubtedly complicate the construction. Even if the object is asymmetrical these lines or planes can be created anywhere and will be useful references.
Making the platform level gives you the option to put a plan view drawing of your object on it and drop plumb lines from any point to the drawing. This is an accurate way to determine if your furniture is twisting or leaning in an unforeseen way.
Having used this method for decades to create curved and inclined planes in my furniture I have come to the conclusion that the time I spend upfront making the endo/ exo structures is easily recovered in time saved fussing, fitting or remaking parts. Even prototype projects are made this way, just not as exact. But it does give me a heads up when I’m making the real thing.
Making chairs
Most dining chairs will fit on a platform 800 x 800mm. This reusable platform is constructed on a stable base that can be anchored to the floor. I recommend the top be made of 25mm thick MDF or two pieces of 12mm ply glued together.
The surface should be at a comfortable working height; for me (height 1775mm) that is 600mm.The platform surface is adjusted to dead level with four 8mm hanger bolts. The adjusting nuts are below the surface so they are never in the way. Use a level diagonally to level the platform. A centreline runs down the middle and is surrounded by 50mm grid lines.
For chairs, the height of the endo or exo skeleton depends on the chair and where the complicated joinery is. Sometimes it’s a combination, an exoskeleton for the back and a short endoskeleton for the seat and arms.
While the platform and base remains the same the skeletons can be quite different. A common, and very important detail is the centreline that moves in three dimensions from front to back, up and over the skeletons. All measurements are made left and right from the centreline but only the measurements from one side are actually used. They will undoubtedly be slightly different (the nature of working with wood). If the dimensions and angles are different sizes the project will begin ‘tilting in the wind’.
Chair Number One is one of Michael Fortune’s best known designs. Dating from 1979 he has now made almost 500 of them. A diagram of endo-skeleton used in their construction is shown below.
Chair Number One
This chair was first designed in 1979 with the view that I would continue to make them in the following years. I’m approaching 500 of these chairs. Again nothing is square or even straight – except the jigs that were made to hold the curved parts. The joinery for the curved crest rail, rear seat stretcher and lower stretcher is all square or parallel to the centreline of the chair. All of the compound angles were picked up from either the endoskeleton or the platform.
A series of left and right square boxes were made to hold the parts in a manner that routers and drill presses could create the joinery. Using the resulting jigs to cut the various joints for a set of twelve chairs makes short work of the fabrication process. That gives me the time to enjoy hand shaping every surface on the chairs.
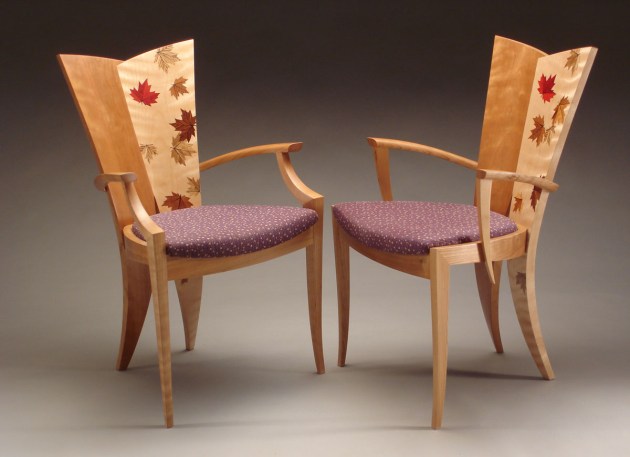
Clarkson Chairs
The first chair prototype for the Clarkson chairs was started with a marginal plan view drawing of the seat to give the splay of the seat frame as it related to the centreline. That led to an endo skeleton that positioned the steambent seat frame and front legs. It was positioned by using the routed out hole in the plywood that later supported the upholstery.
The top of the endo skeleton tilted back at 5° to make the seat more comfortable. The bent seat frame splayed away from the centreline and the legs canted back 3°. An angled plywood interior floating tenon provided the necessary strength for this critical joint. The curved front stretcher was doweled to the inside of the bent seat frame so it did not interfere with the existing tenons joining the seat to the front legs.
The angles for the front stretcher were taken right off the endo skeleton and cut on a drop saw. The back was a vacuum formed compound shape that had to attach to the rear of the bentwood seat frame. Both shapes were anything but square. To solve the problem the holder for the chair back within the exoskeleton slid forward as the various surfaces where hand shaped until a perfect fit was made. Trying to mate the surfaces without the controlled movement provided by the exoskeleton would surely mean the back angle would not be consistent from one chair to the next.
Tables of all types
Tables are made in all sizes. The platform should be larger than the object by at least 250mm all around. This allows for attaching an exo framework should it be necessary. Originally I made the platform as a custom item for each table. Experience showed me that most side tables would fit on platform 800mm wide and 2300 long. Dining tables often used a platform 1500 x 2500mm. Whatever the size of the platform it has to be a reliable, stable and level surface. Again the workable height off the floor should be about 600mm.
The actual height of the endo or exo skeleton is determined by the design of the table which should take into consideration the base that supports the top. Most frequently my skeletons come up to the underside of the top. Cut outs or add-ons accommodate the structure that makes up the base.
Angles for the flowing lines and curves of the Birds Wing Table were determined through the use of both endo and exo skeleton structures.
Bird’s Wing side table
This table was made by joining three curved vacuum formed panels. All were the same radius. An exoskeleton located the curves and held each in a manner that I could determine the angles for joints cut on the tablesaw. Using the centreline to measure the symmetrical intersections was very important for this piece. The rear curve was perfectly upright but as soon as tapers were cut on either side it meant the joining side parts were tilted.
Tablesaw jigs were made to cut the long mitres. The size of the jigs and the angle of the tablesaw cut were determined by the measurements taken from the exoskeleton. The top of the exoskeleton was flat, important because the underside of the top installed later was flat. A flush cut saw was used on the top of the exoskeleton surface. Two layers of tape keep the saw slightly off so any imperfection could be block planed.
The joint faces and mortises between the front legs and the side curves were also done with the curves trapped in the exoskeletons. Biscuits were used here for the joinery. The angles for the clamping cauls came right off the endoskeleton.
The skeleton structure for the Bird's Wing side table starts with supports screwed to a platform marked with 50mm grid lines.
Plan view and constructional diagrams show how the vacuum formed panels are both angled and twist.
The halves of the exoskeleton double as tablesaw cradles for cutting their long mitres at angles which vary according to their tilt.
The halves of the exoskeleton double as tablesaw cradles for cutting their long mitres at angles which vary according to their tilt.
Cutting mitres on the centre panel, once again using part of the exoskeleton as a cradle on the tablesaw.
Leaf Dining Table
The top on this table is a rather unusual shape, the centreline here is at an angle which is symmetrical from the points at either end. The table was drawn full size on paper drawn which was taped to the platform.
The Leaf Dining table has a steambent walnut frame and torsion box top veneered in figured sycamore with marquetry detailing.
Every shape or joint was measured from that centreline which in turn was plotted on the platform. I used a piece of thin straight grained wood to draw the curves. That said, it would always bend differently every time I used it. The grid on the platform gave me the ability get perfect symmetry to the diagonal centreline.
Showing the almost complete base and torsion box top understructure.
The curves on the floor are steambent walnut, 50 x 65mm thick. The apron was about the same dimension but the angled cross section shape was bandsawn after the wood had set. I steam bend solid wood in a manner that gives me identical parts exactly to the form that I have made.
Diagonally opposite and identical ‘legs’ were steambent and joined with angles lifted directly from the exoskeleton.
From a full size drawing every shape and joint was measured from a centerline and plotted on the exoskeleton platform.
Diagonally opposite legs are identical in shape and joinery. I only had to figure out the joinery on two not four because the endoskeleton provided that level of accuracy. I rarely knew any numbers for various angles because I lifted the angles right from the exoskeleton with the adjustable bevels and moved the bevels to the drop saw. A test cut was made to confirm the angles before cutting into the expensive walnut.
Geneva sofa table
There were two centrelines on this project, one for the front view and one for end view. Both provided critical measuring points. I started with a full size drawing because all of the curves required bending forms.
Geneva sofa table – catenary curves for the central support were drawn from a suspended chair and once again full size drawings were used to produce the support skeletons shown below.
The endoskeleton helped me relate the shapes and curves that were located on the floor with those that were attached to the tabletop. The curves all converged in one place so it was important to locate them precisely.
Why I make things
I design and make furniture from the perspective of wanting to explore forms, details and techniques that I would like to know more about. When I’m sketching ideas I am looking for new forms that interest me, not one that I already know how to do. Each piece I make is part of a puzzle for me about the furniture making, the joyous reality is the puzzle will never be completed, there’s always more to learn.
Michael Fortune is an internationally renowned Canadian furniture designer maker and also a highly regarded teacher. From October 6 to 10, 2025, Michael will conduct a five day chair design masterclass at The Coburg Studios, Victoria. Learn more at www.wooddustaustralia.com.au Learn more about Michael Fortune at www.michaelfortune.com